監査で製品の不一致に遭遇したとき
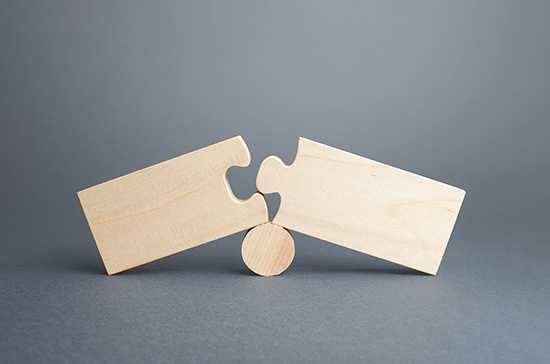
Photo credit: bymuratdeniz
Quality + Engineering 社の代表取締役であり、技術責任者 であるGreg Hutchins氏は、あるプロジェクトにおいて製品の重大な不一致に取り組んだこと、それがどのように全社的な改善につながったかを教えてくれました。
関係者を守るため、名前は明らかにはしていませんが、以下のお話しは実話を元にしています。
ジレンマ
私たちの会社が、数十億ドル規模の企業との契約を結び、9年目となったときのことです。米国にあるそのクライアント企業は、サプライヤーの品質を含む、品質全般に関する事項を私たちの会社に依頼していました。ですから、私たちには、すべての供給された製品が契約上の要求事項と製品仕様を満たしていることを確認にする責任がありました。
以前の入荷検査では長年にわたり適合していた、品質に影響を与える電気部品がありました。その部品の寿命は40年とされていました。しかし、日本のサプライヤーが設計製造したその部品が、現場で早々に故障し始めたのです。
現場での故障、交換、ダウンタイムに非常に大きなコストがかかっていました。すでに40年の実績がある製品であったため、AQL (Acceptable Quality Level 合格品質水準) 1%を基準に受入寸法検査を実施していました。しかし、現場での不具合は増加の一途をたどっていました。その結果、クライアント企業から、技術責任者自らが日本に行って、根本的な原因を究明し、問題を最終的に解決するよう依頼されました。
私は、Quality + Engineeringの代表取締役 兼 技術責任者として、いくつかのティア2のサプライヤーを含む、高度に自動化された日本のサプライヤー (以下サプライヤー) の工場を訪問しました。それは、最先端の製造施設でした。そこにはロボットがあり、製品を持ち上げ、ロボットコンベアに載せて搬送していました。品質管理は完全に自動化され、米国のクライアント企業 (以下クライアント企業) の設計図に指定された各々の重要な寸法の統計的工程管理 (SPC) の表が作成されていました。生産工程での人間の介入は最小限に抑えられていました。
通訳を交えて、企業レベル、プロセスレベルから製品レベルに至るまで、サプライヤーの監査 (forensic audit) を実施しました。企業及びプロセスの主要な管理をチェックしました。財務情報、取締役会への機密の内部監査報告書、内部品質監査、コストのデータ、プロセスのデータ、ISO 9001 の認証書、是正処置要求/予防処置要求、SPCチャート、不合格品の調査、改善グラフ及びワイブル曲線を調査しました。また、第三者機関と契約し、製品の物理的・化学的試験を実施しました。すべてのプロセスと製品の試験はクライアント企業の仕様書に適合していました。では、いったい何が起こっていたのでしょうか。
監査の最終日、私たちは製品の出荷と取り扱いをチェックするために名古屋港を訪れました。港湾職員は、私たちをサプライヤーの従業員だと思い込み、構内の別の建物に連れて行ってくれました。すると、サプライヤーは「Made in China」の同じような製品を持ってきて、梱包しなおし、出荷用の木箱に「Made in Japan」と印をつけていることが判明しました。
これを発見し、私たちは頭を悩ませました。この問題をどのように報告し、解決したらよいのか。
解決策
クライアント企業の契約では、供給される製品は100%「Made in Japan」であることが明確に要求されていました。クライアント企業は、中国から日本に、そして米国に輸送された製品の「Made in Japan」の信頼ラベルに60%のプレミアムを払っていたのです。
このような状況は、クライアント企業に、サプライヤーに、そして私たちの会社に難題を投げかけました。意思決定と権限の点で見ると、私たちは日本の製品が設計図や仕様書に適合していることを確認する責任を負う品質エンジニアリングの会社でした。最終的に、サプライヤーを決定する責任はクライアント企業にありました。これは、世界的にみても、民事的、さらには刑事的な意味合いをもつ、極めて解決の難しい問題でした。あなたならどうしますか?
クライアント企業は、これをどのように取り扱うかを私たちに告げましたが、この企業は、企業レベルのリスク決定を、政治、リスク選好、文化的な配慮、供給される製品の要求事項、事業継続要求事項に基づいて行っていました。最終的な戦略的結論は以下でした。
- クライアント企業はそのサプライヤーをそのまま維持した
- クライアント企業は報復や、訴訟を行わなかった
- サプライヤーは反省していた
- クライアント企業とサプライヤーは、試験、現場での故障、交換、ダウンタイムに対する補償について交渉した
- クライアント企業は数年間、日本製品を購入した
- 中国の業者は製品の設計と製造を改善した
- 結局、数年後には中国が製品の優先的、かつ主要なサプライヤーとなった
- クライアント企業は最終的に、「Made in China」の製品にはより低い価格を支払った
戦術的な品質の観点から、私たちの会社では次のようなサプライヤーの是正/ 予防管理を実施しました。
試験―日本の第三者機関による定期的な、構造的、物理的、化学的、信頼性に関する製品試験を実施した
検査―寸法検査はますます厳しいAQL (合格品質水準) で実施された。
エンジニアリング―サプライヤーは製品の有限要素解析を行い、有限要素解析はピアレビューを受けた。製品の変更はクライアント企業と私たちの会社がレビューし、承認した。
信頼性―サプライヤーは、ワイブルや類似の信頼曲線のみならず、他の顧客からのデータ (無属性) を集計したものも提出した。
生産―サプライヤーは、クライアント企業に生産管理、SPC、最初の製品、及び品質管理計画を提出した。
出荷―遅延や原産地証明を監視するため、コンテナには無線周波数識別 (RFID) のタグが付けられた。
この話から持ち帰った極めて重要な教訓は、解決策は、是正処置要求を挙げることでも、ISO 9001の認証を取得することでも、品質ツールを使うことでもなく、企業ベースの事業戦略に帰するものであったということです。これにより、私たちは、クライアント企業の視点に立って、問題のありかと文脈 (context) を理解することの重要性に気付かされました。
※ これは、CQI|IRCAのメンバーから寄せられた『クオリティプロフェッショナルのジレンマ』に関するシリーズ記事の1つです。監査だけではなく、マネジメントシステムに関する活動でジレンマを感じた経験をお知らせください。皆様からのご連絡をお待ちしています。