プロジェクトにおける品質とリスクのマネジメント
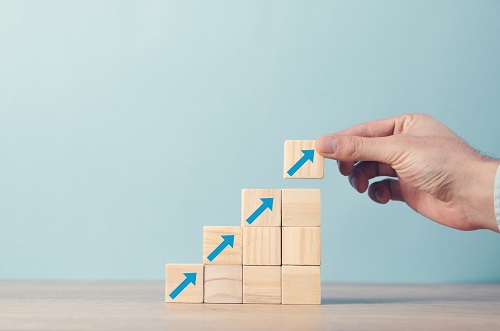
Photo credit: oatawa
石油・天然ガスの多国籍企業であるサウジアラムコのProject Inspection Supervisorである Abdullah Shaiban氏は、リスクを品質マネジメントシステムに組み入れることが重要であるとしています。
ISO 9001:2015は、組織が品質マネジメントシステム (QMS) を持続可能な開発のソリューションに展開し、事業全体のパフォーマンスを改善するために適用する際の枠組みを提供しています。パフォーマンス向上の結果は、プロジェクトの個々のプロセスに対して一連の活動を順々に実施することにより生み出されます。これらの活動は、品質目標を達成するための継続的改善を活用した、証拠に基づく意思決定 (evidence-based decision-making) に基づいています。
この枠組みは、多くの産業で採用されています。例えば、石油・ガス施設の建設プロジェクトでは、品質目標を達成するためにQMS が要求されます。この目標を達成するために、組織内で (ISO 9001:2015のような) 持続可能なQMSを実施するための特定のプロセスの有効性を決定する際の主要業績評価指数 (KPIs) が開発されています。KPIは不可欠です。なぜなら、KPIを用いて事業目標を意思決定の最前線に据えることにより、プロジェクトマネジャーが手元のプロセスの有効性を測定できるようになるからです。
リスクは、プロジェクトの目標 (例えば、範囲、スケジュール、コスト及び品質など) に影響を与えるので、QMS を構築する際に考慮しなければなりません。リスクとは失敗や損失を引き起こす可能性のある潜在的な脅威であり、特定のプロジェクトに悪影響を及ぼすかもしれません。したがって、品質目標を決定する際にはリスクを組み入れ、KPIを通じて監視します。KPIには、作業合格率、不良設備項目数、保存不良率、溶接修理率 (WRR = welding repair rate) などがあります。これらのそれぞれについて、リスク低減要因に基づき品質目標が設定されます。
品質パフォーマンスは、さまざまな指標により測定することができますが、その1つにプロジェクト品質指標 (PQI = project quality index) がありますが、これはQMS の実施の有効性や、必須の規格や規則に対するプロジェクトのコンプライアンスを測定するためのパフォーマンス指標です。例えば、石油・ガスプロジェクトは、設計、調達、建設の3つの主なフェーズで実施されます。このプロジェクトのフェーズごとに、事前に定義された品質目標値と品質目標(quality goals and objectives) に向けた進捗状況を測定するための品質関連KPIが作成され、品質KPI の加重平均スコアの合計がPQI を算出するために使用されます。
継続的改善の監視
KPIを継続的に監視することにより、プロジェクトチームは製品やプロセスについて報告された欠陥に対処するために迅速に行動することができます。是正処置だけでなく、シックスシグマ、リーン、カイゼン、デミングのPDCAサイクルなどの継続的改善のためのツールを活用し、持続可能な結果が得られるようにすることが大切です。ISO 9001:2015規格は、4つのフェーズの反復的なアプローチによりプロセスを強化、改善するPDCAサイクルを利用しています。PDCAサイクルは、プロセスが十分に資源提供され、維持され、組織が改善の機会を効果的に捕捉することを確実にします。
石油・ガス産業におけるケーススタディ
ある石油・ガスのメガプロジェクトでは、請負業者と協力してプロジェクト遂行中にPDCAサイクルを実施しました。目標値として、11%あった溶接不良率 (WRR = welding rejection rates) を品質目標である5%にすることを目指しました。
「Plan」のフェーズは、プロジェクトの核となる課題を明確にすることから始まりました。目標値は、要求される目標に応じて設定され、利用可能な資源に基づいていました。計画は、事前に定義されたKPI からの逸脱の可能性を最小限に抑えるため、すべてのリスク軽減要因を考慮する細々としたステップから成っています。チームは、WRR が高くなる根本原因を特定するために、毎週の溶接修理、欠陥分析及び溶接工のパフォーマンスレポートなど、このタスクを遂行するために必要なすべての重要なレポートを一元化し、分析しました。
この分析には、チェックリスト、根本原因分析、魚の骨図 (特性要因図)、5つのWと1Hの方法論など、多くの品質ツールやテクニックを利用しました。これらのツールを利用した結果、高いWRRを引き起こした潜在的な要因は、溶接工のスキルセット、溶接機器、アルゴンガスの純度、溶接消耗品であることが判明しました。
「Do」のフェーズでは、制御された環境で小規模な実験を行うことで、どのような要因が広く存在するかを特定するための計画を盛り込みました。経験年数の異なる5名の溶接工に、それぞれ、同じ溶接技術を用いて、複数のタイプの配管材料の継手を30個溶接させました。その結果の継手について、X線写真を用いた溶接部の試験を実施し、溶接された継手の合格率と欠陥の種類を検証しました。この実験により、この問題の根本にある原因が明らかになりました。
「Check」のフェーズは、PDCAサイクルの中で、おそらくもっとも重要なものです。このフェーズでは、計画の実行状況を監査し、ミスが再発するのを回避できているかを確認します。さらに、根本原因を洗い出して、無関係なものを排除することが可能になります。前述のケーススタディでは、溶接工ごとの欠陥の種類と頻度を特定するために、ポロシティ/空洞 (porosity)、不完全融合 (incomplete fusion)、及びルートへこみ (root concavity) のマトリックスを作成しました。その結果、もっとも頻繁に発生する欠陥のタイプはポロシティであり、これは使用されるアルゴンガス中の不純物が原因であること、また、溶接機械の校正が行われていないために、不完全融合やルートへこみのある継手がいくつかあることが明らかになりました。また、経験が少ない溶接工ほど、溶接に欠陥が多いことも指摘されました。
最後の「Act」のフェーズでは、前のフェーズで得られた結果に基づいて対応を行いました。是正のための対策が特定され、プロセスに組み込まれました。溶接工に対しては、必要に応じてより優れたスキルセットを得るために、毎週のトレーニングプログラムと作業前のミーティング (toolbox meeting) を実施しました。さらに、モックアップの継手を使って、アルゴンの純度を定期的にチェックしました。最後に、すべての溶接機器の校正要求事項を記録しておくための新しい校正システムを確立しました。
メリットと成果
このプロジェクトでは、WRR 5%をターゲットとした品質目標を満たしたというだけでなく、コストを535,040米ドル削減し、6か月のスケジュール遅延を防ぐことができました。
したがって、品質マネジメントシステムにリスクを組み込み、継続的改善のツールを適用することは、以下に役立つと言えます。
- 予防と継続的改善に先回りして対応する文化を確立する
- 影響を最小限に抑え、利益を上げる
- 最終製品の品質を確実に高める
- 課題及び機会を予測する
- 顧客満足を高める
- プロセスのパフォーマンスと効率を向上させる
継続的改善を実施し維持すれば、リスクを組み込んだ品質マネジメントシステムは成功するでしょう。継続的改善のツールは事前に定義された品質目標に準拠した結果をもたらし、将来にわたり逸脱の再発を減らすことができる予防策を開発するのに役立ちます。