日本の品質は本当に地に堕ちたのか: 岩本威生氏に聞く (パート1)
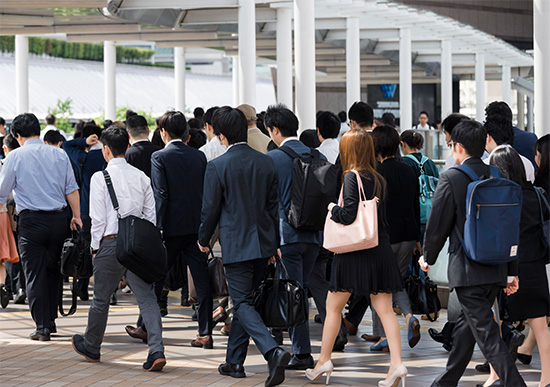
ISO/CASCO (適合性評価委員会) 国内委員会委員、JISC適合性評価部会の専門委員会委員などを歴任されるとともに、日本のマネジメントシステム適合性評価制度の確立、並びに普及、啓発活動に実地で取り組んでこられた日本化学キューエイ株式会社の岩本威生氏に、一連の品質不祥事の報道を受けて喧伝される日本の品質の劣化という言説について、また、これからの審査/監査のあり方についてなど、その幅広い知識、経験に基づくお話を縦横無尽に語っていただきました。
一連のデータ改ざん/ねつ造は製品品質の問題なのか
IRCAジャパン 竹内: 日本を代表する企業に長年勤務され、その後認証機関で数多くの企業に接してこられ、また、2013年に我が国のマネジメントシステム適合性評価制度の確立及び発展への貢献を認められて経産大臣表彰を受けたお立場から見て、日本企業におけるデータ改ざんやねつ造など、一連の不祥事を聞いたとき、どのように感じましたか。
メディアの上では、日本の品質は地に堕ちた、日本の品質はどこに行ったという論調もありましたが、本当にそうなのでしょうか。
岩本: 「データの改ざん/ ねつ造」が本当に不適切な品物をお客様に納入していたということなら、確かにけしからんことで、その企業は断罪されるべきです。ですが、本当に製品そのものに問題があったのでしょうか。例えば神戸製鋼所の例では、元々、不祥事の問題公表が顧客から製品の品質についての指摘があったからと言うことではなく、経団連でいろいろ品質問題があるから各社、自分たちで調べるようにという通達があり、自ら不適切行為が行われていないか点検しているうちに発見されたということでしたが、何か第三者的な調べ方しかしていないのですよね。
正直な話、経営者はなんであんな公表の仕方をしたのか、経営者は自分の会社を愛していないのだろうか、理解していないのだろうかという思いが私は強いですね。
竹内: でも、不正なことをしていましたと自ら公表することは正しいことではないのですか。会社を愛していない、理解していないというのはどういう意味でしょうか。
岩本: 別におかしなことを隠すとか、かばうという意味ではなくて、自分たちの仕事を理解して、一所懸命仕事をしている人たちをおかしな立場に立たせないように守ってあげるのが、やはり上の仕事だと思うのですね。
経営者が現場のことを知らず、自分たちが現場をマネジメントできていなかったことを棚に上げて、コンプライアンスを重視していますとばかりに、現場を責めても何も解決にならないと思うのです。ただ、自分たちのブランドを自分たちで貶めてるだけ、現場の従業員を苦しめるだけだと。
お客様にしても、品質不祥事だと言われたら、自分たちが変な品質のものを受け取ったということになるではないですか。そう言われたら、自分たちの取引先に何か説明しないといけなくなる。実際にはおかしな製品を作った訳でもないのに、なんでそんなことをさせられなければならないのかと思いますよ。
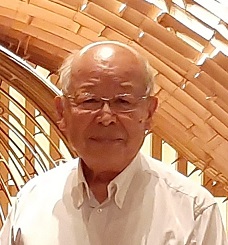
竹内: では、問題はどこにあると考えておられますか。
岩本: 2017年12月5日の日経ビジネスオンラインに、池谷由香記者が「『モラル低下』『品質への甘え』で片付けてはいけない」と題する記事を書いていました。池谷記者はある大手自動車メーカーOBを別件で取材していたときに、そのOBが堪りかねた様子で不意に記者たちに「あなたたちメディアはすぐに『品質問題』『日本のモノ作りの失墜』って話にしたがりますがね、実際はそうじゃない。あれは品質の問題じゃなくて、管理とかマネジメントの問題ですよ。あの不正があったせいで、実際の品質問題が出ていますか? ないですよ。それも分かっていないのに品質軽視だ、日本の品質低下だとまくしたてるからおかしなことになる。そうじゃないですか?」と逆インタビューを始めたそうです。
池谷記者は、問題は経営者が現場のことを知らなすぎることにあるのではないか、これはあとで説明しますが、現場には建前の数値と本音の数値が存在しているのに、そうとは知らずに現場の失態を責めて、コンプライアンスの徹底ばかり、それがどんなに現場を心理的に苦しめているかも気づかずに強調しているところに問題があると指摘しています。
竹内: 同様の意見は他にもありますか。
岩本: ええ、長くトヨタ自動車で仕事をし、今は国際コンサルタント会社クレアブの日本代表をつとめる土井正己氏はネットマガジンのビジネスインサイダージャパンの2018年2月21日の記事に「世界が報じた『日本品質の劣化』は大きな誤解、不祥事招いた日本企業の3つの弱み」と題する主張を論説で展開していますが、その中で土井氏は、「契約に対する認識の甘さ」「トップダウンとボトムアップの連携の弱さ」「危機管理の粗さ」を3つの弱みとして指摘している。これは池谷記者の指摘と重なっています。
同様に、企業法務やコンプライアンスに詳しい、元検事で弁護士の郷原信郎氏は自らのブログで、「このような『データ改ざん』の殆どは、実質的な品質の問題や安全性とは無関係の『形式上の不正』に過ぎず、顧客に対して『データ書き替え』の事実と、真実のデータについて十分な情報を提供し、書き替えに至った理由や経過を正しく説明して品質への影響や安全性の確認を行うことができれば、もともと大きな問題にはなり得ない。」と指摘しています。
ここで持ち出したお三方の考え方は、マテリアル製品における品質検査結果の書き換え問題は実は最近起こった問題ではなく、ずーっと以前からあった現実的な慣行で、問題は経営者、管理層の認識がものづくりの現場から遊離して、建前のコンプライアンスばかり振りかざすようになったためだと指摘していると思います。 そして、私も同様の意見の持ち主です。
マテリアル系の品質仕様の難しさ
竹内: なるほど。現場やそこで働いている人々をよくご存じの岩本さんが憤りを感じるお気持ちもわかるような気もしますし、品質の問題や現場の問題というより、日本の組織のマネジメントのあり方の問題という見方にも興味が湧きます。
それにしても、そもそも、現場に建前の数値と本音の数値という二重の基準があるという問題はあるわけですよね。建前の数値と本音の数値がなぜ存在するのですか。
岩本: 神戸製鋼所もそうですが、マテリアル系では、品質仕様は暫定的な、建て前的なもので、本当の品質は試作品を評価してもらって、それでいいかどうかということを見る。それで試作品そのものが仕様ということになりますが、それを仕様書としてどう表すかということがなかなか難しいのです。
マテリアルの場合、製品メーカーはマテリアルメーカーから納入されたマテリアル製品をそのままで製品に組み込むことはほとんどなく、何らかの方法で形を変えて使うため、製品メーカーが使用マテリアルの納入(受入)品質を定義することは困難です。一方、マテリアルメーカーはマテリアルがどのように製品に使われるか詳細はわからないことがほとんどですから、納入先であるお客様の立場での品質仕様を決めることは困難です。そこで、お客様のお話から、最適なマテリアルのレシピー、製造方法を推定して、試作品を作り、お客様による何度かの試作品評価の後、適切な試作品が決まれば、その試作品の品質仕様を決めて取引契約を取り交わすことになります。その際に、マテリアルメーカーでは、お客様がマテリアルの受入時に検証できるように、お客様では検証のしようがないレシピーや製造方法ではなく、マテリアルの強度、硬度、あるいは粘度などといった製品を定義するための項目を代わりに提案し、試作品の検査データから仕様を提案することになります。
竹内: 今回、問題になっているのは、その決められた仕様に沿っていないデータを仕様に沿うように改ざんしていたということですよね。
岩本: 仕様を決めるのは難しいのです。大体仕様を決めるのは技術系、特に開発研究所のようなところがやっていますが、そういうところは開発の生産性をできるだけ上げるために早くきりを付けたい。一方、お客様にしてもいいものであると評価したら、できるだけ早く使いたい。仕様の限界として決めた値も本当に限界と見極めて決めることもまれだと思います。そして、これだなと思って仕様に決めたものが実は違った、ずれていたということがあります。マテリアル系の場合の検査はいろいろ前処理をした上でデータを測ったりなどしますから、試験台の上に置いてパッとやったら出てくるという検査ではないのですね。前処理がずっとあって、その結果、測る。その前処理の影響も全部、不確かさの中に入っている。そうすると、これはかなり人的な寄与もあって、データがずれてしまうことがあるのですよ。会社の中で現場の検査データと開発部門の検査データにどの程度バイアスがあるのか、そのバイアスを見て、決めをどうするかという会社の中での標準管理をちゃんとしなければいかんのを、あまりそこまでやっていないところが多いのですね。まあ、それも問題なわけですが。
竹内: 仕様で決めた上限、下限の値が実際の値とずれていたと分かったらどうなりますか。
岩本: 現場としては、営業部が入って、開発部隊も入って、お客さんのほうの技術者と話して、これでお互い行きましょうと決まった仕様を、あとで、いや、ちょっとあれ、違ったんですというのは言いにくいですよね。反対に、お客様側もこれで決まったと、会社の中のいろいろなところに連絡をした。あれ、違ったんだと言われても、やはりちょっと社内の立場上、気まずいですね。だから、お互い阿吽の呼吸でやるところが出てくるのですね。さらに開発部隊のテーマをできるだけ早く移管したいという事情があって、現場の試験機器を使わずに研究所の試験機器を使ったデータだけで仕様を決めて移管してしまうとかね。あるいは確認のためのロット数が少ないとか。ただし、お互いそういう事情が分かるので、今回、検査結果が仕様からちょっとずれているのですけど、ものは一定の条件でつくっているから、使えないかどうか、ちょっと確認しながら使ってくれませんかと言って、では、いっぺん、評価しますと言って使ってくれることがありますね。でも、検査結果の成績表を付けていると、受入のほうのところでこれ、仕様とずれているじゃないかということで撥ねられるから、それがないようにそのデータちょっと変えておいてちょうだいよという話をお互いやるんですね。そこで、建て前の数値と本音の数値ともいうべき二重の基準ができてしまうのです。
本音と建て前を解消するために
竹内: しかし、これは本来は国内でももちろん正当化できないことだと思いますし、なおのこと、国外では通用しないのではないですか。
岩本: もちろん、契約社会の西欧にあって契約を軽視して現場が判断するということは、契約締結部門と実行部門の協調がとれていないということで、会社全体の信用を落とすことになり、許されないことだと思います。ですが、開発あるいは技術検討段階から営業生産への移管初期に、お客様の事情で移管をせかされるなど、少ない生産実績で品質仕様を決めざるを得ないなどの状況は海外でも共通にあり得ることです。このようなとき、西洋の組織では品質仕様をまず暫定仕様として契約し、実績データが集まってから本仕様を決めるということで、建前だけの仕様を作ることを回避するのが普通だと思います。一方、そのような対応を製造部門に押しつけるのは不確定な製品の生産が製造部門に押しつけられることになるので製造部門は拒否することが通例だと思いますので、本仕様が確定するまでは生産は開発部門あるいは技術部門の責任下で行うのが原則になっていると思います。これによって現場にコンプライアンスを守らせるシステムができます。
ところが残念ながら、日本では全員参加を強調する中で、このようなシステムが育ってこなかった、経営陣が育ててこなかったひずみの影響が、短期成果を追い求める時代を背景に出てきたのが一連の問題のように思います。それが、これは品質の問題ではなく、経営やマネジメントの問題だという主な理由です。
竹内: なるほど。
岩本: 余談になりますが、私はかつて日本の代表的な自動車メーカーの品証部長さんにマテリアル製品の品質仕様についてお話を伺ったことがありますが、その時、彼は自分たちにはマテリアルの品質仕様についてはイニシアティブをとって決める能力はありませんとはっきりおっしゃいました。ただし、マテリアルメーカー主導で契約した品質仕様に絡む問題が実際には出たときにはなぜ問題が出たかについてきっちり話をさせてもらうことになりますから、とも付け加えられました。そして、そもそも品質仕様のデータにロット数などから自信がないのだったら初めから言ってほしい。自信があると思うから、それを受け取って、その仕様データを設計図の中に盛り込んでいるのですね。そうすると、5年間か何かで型式が変わらない限り、その設計図は変えない。変えないから値を変えるわけにいかない。でも、初めから暫定だと言ってくれたら、設計図に暫定データと入れて、あとでそれを修正する、それは不可能ではない。だから、ちゃんと言ってほしいとおっしゃっていました。とはいえ、すべての自動車メーカーがそういう考えをもっているわけでもありませんし、納入者の立場からそのように言うのは難しいことです。
しかし、お互い、そういう可能性を認め合いながら、より現実的な商売の取り決めができるような形にもっていかないといけないということを理解し合ったら、やりやすい世界になるのだろうと思っています。
竹内: これは私がちらっと聞いた話ですが、海外の企業では長大な仕様の指定が契約書に付いていることがあるのに、それを請け負った日本の会社はそんなものは全然見ていない。何かあったときに、向こうから来て、例えばデータなりなんなりを見せろとか何とかとなったときに中身さえも見ていない、そういうものが、へー、あるんですかというような会社もまだある。
岩本: ありますね。
それに私なんかもそういう仕様書の経験はありますよ。仕様書に検査項目が10何個あるのですね。その中に例えば、屈折率なんてのがあるんですよ。何かの物質について、これは屈折率がいくつだというのは物性表に載っているのですよ。相手さんはよく知らないから、そういう一般的な性質を調べて、それを仕様書の中に織り込んでくるのですね。こちらのほうは、なんで、こんなものまで毎回検査をやらなきゃいけないのかと思っても、そういう仕様書に織り込んであるものは全部やらなきゃいかんとみんな頭から思い込んでいた。
しかし、これは保証項目です、いつ確認していただいてもこの値になるということです。疑問があったらいつでも測定しますから、最初の3ロットくらいまでは測定しますけれども、以降は測定を省略させてください。こちらのこれも保証できますが、ご心配はわかりますから、これは3か月に1回測定することにさせてくださいとかね。これは、当然ながら毎回やらなければいかんことだと我々も考えていますから、毎回測定します。それで、そういうように保証項目、3か月に1回測定項目、毎回測定とちゃんとつくって、それで仕様書を変更するのです。そうすると、お互いにすっきりした形で仕事ができるんですね。
それを発注元に言わずに請け負ったほうだけで勝手にやってしまうと、後ろめたさがあるし、やっていないじゃないかと言われたら、申し訳ありません、やっていません (笑い) ということになるんですね。やはりそういうお互いが了解した形での見直しや変更を、ごく自然な形でやれるものの考え方を取り込んでいかないといけないと思っています。
竹内: どうですか、それはまだ道は遠いですか。それともだんだんそういうようになってきていますでしょうか。
岩本: まあ、だんだんそうなっているのではないかと思うのですけれども。ともかく、私がやった仕事では会社の中でそういう形で切り替えてきました。
パート1終わり